Have you ever wondered why the price of cement in Nigeria keeps fluctuating? Cement is one of the most essential construction materials in the country, and its cost directly impacts the economy. From building homes to constructing infrastructure, cement plays a vital role in shaping Nigeria's development. But why is it so expensive? Let's dive deep into this topic and uncover the reasons behind the rising price of cement in Nigeria.
Understanding the price of cement in Nigeria isn't just about numbers; it's about understanding the factors that drive these numbers. From production costs to government policies, several elements come into play. Whether you're a builder, homeowner, or just someone curious about the construction industry, this article will give you all the insights you need.
So buckle up and get ready to explore the world of cement pricing in Nigeria. We'll cover everything from the current market trends to the challenges faced by manufacturers and consumers alike. By the end of this article, you'll have a clearer picture of why cement costs what it does and how it affects the nation's growth.
Read also:Jimmy Ntebekos Daughter The Rising Star In The Spotlight
Table of Contents
- Current Situation of Cement Prices in Nigeria
- Factors Affecting the Price of Cement
- The Role of the Nigerian Government
- Challenges Faced by Cement Manufacturers
- Impact on Consumers
- Market Trends in the Cement Industry
- Forecast for Future Prices
- Possible Solutions to Stabilize Prices
- Import vs Local Production
- Conclusion and Final Thoughts
Current Situation of Cement Prices in Nigeria
As of 2023, the price of cement in Nigeria has been on a steady rise. On average, a 50kg bag of cement now costs around ₦3,500, which is significantly higher than previous years. This increase has sparked concerns among builders and homeowners who rely heavily on cement for their projects. The hike in prices has also affected the overall cost of construction, making it harder for people to afford building materials.
Several factors contribute to this upward trend. One of the main reasons is the rising cost of raw materials and energy. Additionally, the devaluation of the Nigerian Naira has made it more expensive to import essential components required for cement production. With inflation rates soaring, the cost of living has also increased, further complicating the situation for consumers.
Why the Price Increase Matters
The price of cement isn't just a number; it reflects the state of the economy. When cement prices rise, it affects everything from housing affordability to infrastructure development. For instance, many Nigerians who were planning to build their homes have had to delay their projects due to the high cost of materials. This delay not only impacts individuals but also slows down the country's economic growth.
Factors Affecting the Price of Cement
Several key factors influence the price of cement in Nigeria. Let's take a closer look at these factors and how they impact the market.
1. Cost of Raw Materials
Raw materials such as limestone, clay, and gypsum are crucial for cement production. The cost of these materials has been increasing due to various reasons, including transportation costs and scarcity. For instance, transporting limestone from quarries to manufacturing plants can be expensive, especially in areas with poor road infrastructure.
2. Energy Costs
Manufacturing cement is an energy-intensive process. The cost of electricity and fuel directly affects production expenses. In Nigeria, where power supply is inconsistent, many manufacturers rely on generators, which are costly to operate. This reliance on alternative energy sources further drives up production costs.
Read also:Why Ammot Cafegrave Is The Hidden Gem For Coffee Lovers Everywhere
3. Exchange Rate Fluctuations
The Nigerian Naira has been experiencing fluctuations against major currencies like the US Dollar. Since some raw materials and machinery are imported, a weaker Naira means higher costs for manufacturers. This increase in import costs is eventually passed on to consumers in the form of higher cement prices.
The Role of the Nigerian Government
The Nigerian government plays a crucial role in regulating the cement industry. Through policies and regulations, the government can influence the price of cement. For instance, import tariffs and taxes on raw materials can significantly impact production costs. However, the government also faces challenges in balancing the needs of manufacturers and consumers.
In recent years, the government has introduced measures to boost local production and reduce reliance on imports. These measures include tax incentives for local manufacturers and investments in infrastructure to improve transportation networks. While these efforts are commendable, their impact on cement prices has been limited so far.
Government Initiatives
- Tax incentives for local manufacturers
- Investments in road and rail infrastructure
- Policies to promote the use of locally sourced raw materials
Challenges Faced by Cement Manufacturers
Cement manufacturers in Nigeria face numerous challenges that affect their ability to produce cement at competitive prices. These challenges include:
1. Inconsistent Power Supply
As mentioned earlier, the inconsistent power supply in Nigeria forces manufacturers to rely on generators, which are expensive to operate. This reliance on alternative energy sources increases production costs, making it difficult for manufacturers to offer competitive prices.
2. Poor Infrastructure
Poor road and rail infrastructure makes it difficult and expensive to transport raw materials and finished products. This lack of infrastructure not only increases costs but also delays production and delivery schedules.
3. Competition from Imported Cement
Despite efforts to boost local production, imported cement still poses a significant challenge. Imported cement is often cheaper due to lower production costs in other countries. This competition makes it difficult for local manufacturers to compete on price alone.
Impact on Consumers
The rising price of cement has a direct impact on consumers, especially those in the construction industry. Homeowners, builders, and developers are all affected by the high cost of cement. Many have had to delay or scale down their projects due to the increased expenses.
For instance, a homeowner planning to build a house may find that the cost of materials has doubled, making it unaffordable to proceed with the project. Similarly, developers may have to reduce the number of units they plan to build, affecting the availability of affordable housing.
Consumer Strategies
- Delaying construction projects until prices stabilize
- Exploring alternative building materials
- Negotiating with suppliers for better pricing
Market Trends in the Cement Industry
The cement industry in Nigeria is constantly evolving, with new trends emerging every year. Some of the current trends include:
1. Increased Focus on Sustainability
Manufacturers are increasingly focusing on sustainable practices to reduce their carbon footprint. This includes using alternative fuels and raw materials, as well as adopting energy-efficient technologies. While these practices are beneficial for the environment, they can also increase production costs in the short term.
2. Adoption of Technology
Technology is playing a bigger role in cement production. From automated processes to digital supply chain management, manufacturers are leveraging technology to improve efficiency and reduce costs. However, the initial investment in technology can be expensive, which may affect pricing.
3. Expansion of Local Production
With the government's support, local manufacturers are expanding their production capacities. This expansion aims to meet the growing demand for cement in Nigeria and reduce reliance on imports. While this is a positive development, it may take time for the effects to be felt in the market.
Forecast for Future Prices
Looking ahead, the price of cement in Nigeria is expected to remain volatile. While efforts to stabilize prices are ongoing, several factors could influence future trends. These include:
1. Economic Conditions
The overall economic conditions in Nigeria will play a significant role in determining cement prices. If the economy stabilizes and inflation rates decrease, we may see a reduction in cement prices. However, if economic conditions worsen, prices could continue to rise.
2. Government Policies
Future government policies, such as changes in import tariffs or subsidies for local manufacturers, could also affect prices. If the government continues to support local production, we may see a gradual decrease in prices as supply increases.
3. Global Market Trends
Global market trends, such as changes in the price of raw materials and energy, will also impact cement prices in Nigeria. As the world moves towards more sustainable practices, the cost of production may increase, affecting prices.
Possible Solutions to Stabilize Prices
Stabilizing the price of cement in Nigeria requires a multi-faceted approach. Here are some possible solutions:
1. Improve Infrastructure
Investing in infrastructure, such as roads and railways, can significantly reduce transportation costs for manufacturers. This reduction in costs can help stabilize prices in the long run.
2. Promote Local Production
Encouraging local production through government incentives and support can reduce reliance on imports and stabilize prices. By increasing the supply of locally produced cement, the market can become more competitive, driving prices down.
3. Address Energy Challenges
Solving the energy crisis in Nigeria is crucial for stabilizing cement prices. By improving the power supply and reducing reliance on generators, manufacturers can lower their production costs and offer more competitive prices.
Import vs Local Production
The debate between imported and locally produced cement continues to be a hot topic in Nigeria. While imported cement is often cheaper, it poses a threat to local manufacturers and the economy as a whole. Supporting local production not only creates jobs but also contributes to the country's GDP.
However, local manufacturers need to address their challenges, such as high production costs and poor infrastructure, to compete effectively with imported cement. By improving efficiency and reducing costs, local manufacturers can offer competitive prices and gain a larger share of the market.
Conclusion and Final Thoughts
In conclusion, the price of cement in Nigeria is influenced by a complex mix of factors, including raw material costs, energy prices, and government policies. While the current situation may seem bleak, there are solutions that can help stabilize prices and promote the growth of the cement industry.
As a reader, we encourage you to share your thoughts and experiences with cement pricing in Nigeria. Have you been affected by the rising costs? What solutions do you propose? Leave a comment below and let's continue the conversation.
Don't forget to check out our other articles for more insights into the Nigerian economy and construction industry. Together, we can work towards a brighter future for Nigeria's development.

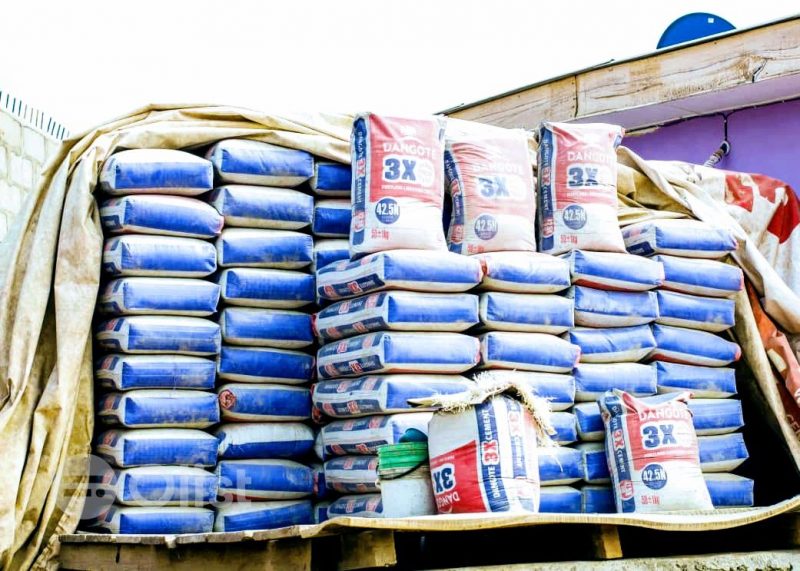
